Achieving Excellence - Quality Principles For Manufacturing
In the fast-paced world of creating things, getting quality right isn't just a nice-to-have; it's truly a cornerstone for enduring success. When we talk about manufacturing, the idea of delivering something reliable, something that truly works as it should, holds a lot of weight. It’s about building trust with those who use what we make, ensuring every item that leaves the factory floor meets a certain high standard.
This commitment to producing top-notch goods influences everything, from the materials picked out to the way things are put together, and even how they are checked before they go out the door. It’s a way of thinking that touches every single step, making sure that what customers get is not just okay, but something they can count on. It’s a core belief, you know, that what you put out there should reflect care and attention to detail, so it’s more than just making a product; it’s about making a promise.
For those involved in bringing products to life, understanding what quality truly means, and how to keep it consistent, is incredibly helpful. It’s about more than just fixing mistakes; it’s about setting up a system where mistakes are less likely to happen in the first place. This approach helps companies not only satisfy their current customers but also build a reputation that brings new ones in, securing a brighter future for the business. So, it's almost like a continuous effort to be better, every single day.
Table of Contents
- The Heart of Making Things Well
- What Makes a Product Truly Great?
- Keeping Things on Track - Assurance Versus Checking
- How Do Quality Quotes for Manufacturing Guide Us?
- Systems That Support Better Work
- What Are the Real Benefits of a Strong Quality Approach?
- Simple Helpers for Everyday Quality
- How Can You Start Applying Quality Quotes for Manufacturing Today?
The Heart of Making Things Well
When we talk about ensuring things are made well, we often hear two big ideas: quality assurance and quality control. These are, in a way, two sides of the same coin, both working to make sure a service or an item meets certain standards. Quality assurance is a bit like setting up the rules of the game before you even start playing. It’s about making sure the process itself, how you go about making something, is set up to produce a good outcome. This might involve planning out every step, making sure everyone knows what they are supposed to do, and having clear instructions. Basically, it’s about preventing problems before they pop up. You know, it’s about being proactive.
On the other hand, quality control is more about checking the actual results. Once something has been made, or a service has been given, quality control steps in to look it over. This could mean inspecting items, testing them, or simply making sure they match what was planned. If something isn't quite right, then the idea is to catch it here before it goes any further. So, while assurance is about the way you do things, control is about the item itself, making sure it holds up. It’s like a final check, really, to make sure everything is as it should be.
For anyone looking to get a clearer picture of these ideas, places like ASQ, a leading society for quality, offer really helpful explanations. They provide clear descriptions and help you see the small but important differences between these two ways of thinking about making things well. It’s quite useful, in fact, to understand how they fit together to create a full picture of keeping things good. They actually have a lot of resources for anyone interested in this topic.
What Makes a Product Truly Great?
What truly makes a product stand out, making it something people really value? Well, it’s more than just meeting a basic standard. A truly great item, a top-tier product, goes beyond simply working; it truly delights the person using it. This means it not only fulfills what someone expects it to do, but it also might have some extra touches, some small details that make it a joy to use. Think about it: an item that just does its job is fine, but one that does its job effortlessly, feels good, and perhaps even looks nice, that’s something else entirely. So, it's almost about creating a positive feeling, not just a functional one.
This higher level of quality, sometimes called "level two quality," suggests that simply satisfying a customer isn't the whole story. It’s about aiming to exceed their hopes, to give them something that feels a bit special. This kind of approach helps build strong connections with customers, turning them into loyal fans who will come back for more. It’s a bit like giving someone a gift that they didn't even know they wanted, but now can't imagine living without. This way of thinking, you know, really shapes how things are made.
Achieving this level of excellence requires a deeper look into what people truly want and need, sometimes even before they realize it themselves. It involves listening, watching, and putting yourself in the shoes of the person who will eventually hold or use what you're creating. This attention to detail, this focus on the user's experience, is what truly sets apart something that is just good from something that is truly outstanding. It's a subtle difference, perhaps, but one that makes a world of difference in the long run, and that is, in some respects, the goal.
Keeping Things on Track - Assurance Versus Checking
Let's get a bit more specific about those two big ideas we touched on earlier: quality assurance and quality control. It's really quite important to grasp the distinction because they serve different, yet equally important, roles in making sure things are made well. Quality assurance, for example, is primarily about the "how." It focuses on the method or the way a process is carried out, or how an item is brought into being. This might involve setting up detailed procedures, training people correctly, or making sure the right tools are available. The aim here is to build quality into the process itself, so that the outcome is likely to be good from the start. It’s like setting up a reliable recipe before you even begin cooking, so, you know, you’re less likely to mess up.
Quality control, on the other hand, shifts its focus to the "what." It’s more about the checking part of managing quality. This involves looking at the finished item or the completed service to make sure it meets the required standards. It’s the inspection aspect, where you might test a product, measure its parts, or simply give it a thorough look-over to spot any flaws. If something isn't right, quality control is where it gets caught. It’s like tasting the food after it’s cooked to make sure it tastes good before serving it. These two concepts, while distinct, actually work together to form a complete approach to making things well, ensuring both the journey and the final product are top-notch.
An alternative way to think about it is that assurance is about building confidence that quality requirements will be met, while control is about fulfilling those requirements. One is about the system, the other is about the result. They are both necessary for a full picture of making sure things are good. You can't really have one without the other and expect consistent, reliable results. They really do go hand-in-hand, and that is, in a way, the whole point.
How Do Quality Quotes for Manufacturing Guide Us?
You might wonder, how do ideas about making things well, like those found in "quality quotes for manufacturing," actually help us in the daily grind of production? Well, these guiding thoughts, often distilled into short, memorable phrases, act like small reminders of what truly matters. They can help shape the way people think about their work, moving them from just completing a task to truly caring about the outcome. For instance, a simple saying about doing things right the first time can really change how someone approaches their work, making them more careful and thoughtful. It's like having a little compass pointing you in the right direction, every single day. So, it's almost like a mental nudge, you know?
These kinds of phrases also help create a shared understanding among everyone involved in making a product. If everyone understands that "quality is everyone's job," then there's a collective sense of responsibility, rather than just leaving it to one department. This shared vision can make teams work together more smoothly, spotting potential issues earlier and finding solutions faster. It fosters an environment where everyone feels they have a part to play in the bigger picture of making something great. It really helps to get everyone on the same page, which is very helpful.
Moreover, these guiding thoughts can serve as inspiration, especially when things get tough. When a challenge arises, remembering a core idea about persistence or dedication to excellence can provide the motivation needed to find a solution. They are more than just words; they are principles that can be applied practically to everyday situations on the factory floor, helping to maintain a consistent focus on delivering the best possible item. They are, in a way, the wisdom of experience, boiled down to something easy to remember and apply. They are, quite simply, valuable little nuggets of wisdom.
Systems That Support Better Work
A quality management system, often called a QMS, is a structured way of doing things that helps an organization make sure its items and services are consistently good. Think of it as a clear roadmap that lays out all the steps, rules, and duties for everyone involved in achieving specific quality goals. It’s not just a vague idea; it’s a detailed plan that defines how things are done, who does what, and how responsibilities are shared to meet certain quality policies. This kind of system helps to organize all the efforts that go into making something, ensuring that nothing important is missed. It's a pretty big deal, actually, for keeping things on track.
These systems play a truly important part in helping companies get better over time. By having a clear framework, organizations can look at their processes, figure out what’s working well, and pinpoint areas where they could improve. It’s a continuous cycle of learning and adjusting, always striving to make things a little bit better than they were before. For instance, a QMS can help a business track how many items meet standards, or how quickly issues are resolved, giving them clear information to act on. So, it’s more than just a set of rules; it’s a tool for ongoing improvement, which is very useful.
Learning about the background and advantages of a quality management system can really open your eyes to how much of a difference it can make. Places like ASQ have lots of information on this, explaining how these systems have developed over time and the many ways they help businesses succeed. They show how a well-thought-out QMS can lead to fewer mistakes, happier customers, and a more efficient way of working for everyone involved. It’s a bit like having a solid foundation for your entire operation, allowing you to build something truly strong and lasting. It is, basically, a strategic approach to making things better.
What Are the Real Benefits of a Strong Quality Approach?
So, why go through all the effort of putting a strong quality approach into practice? What are the actual upsides for a business? Well, the advantages are quite significant and touch many different parts of an organization. For starters, when you consistently produce good items, your customers are likely to be much happier. Happy customers tend to stick around, become repeat buyers, and even tell their friends about your great products. This word-of-mouth advertising is, in a way, the best kind of promotion you can get. It builds a solid reputation, which is incredibly valuable in the marketplace. You know, people trust what their friends say.
Beyond customer satisfaction, a strong focus on quality often leads to more efficient ways of working. When processes are clear and everyone knows their role in maintaining standards, there are fewer mistakes, less waste, and less need for rework. This saves time, materials, and money, making the entire operation more cost-effective. It's like running a smoother machine, where all the parts fit together perfectly, reducing friction and increasing output. This kind of efficiency can give a business a real edge over its competitors, which is very important.
Furthermore, a commitment to quality can help a company meet various industry standards and regulations, opening up new markets and opportunities. It also creates a better working environment for employees, as they can take pride in the items they produce and feel confident in their work. This can lead to higher morale and lower staff turnover. Ultimately, a strong quality approach isn't just about making better items; it's about building a healthier, more successful business overall, one that can stand the test of time. It's a long-term investment, basically, that pays off in many ways.
Simple Helpers for Everyday Quality
For anyone looking to get started with making things better, there are some really straightforward yet powerful tools available. These are often referred to as the "seven basic quality tools," and they have a few different names, like the "old seven" or the "classic seven." Regardless of what you call them, they are simple ways to help understand and improve how things are made. These tools don't require fancy software or deep technical knowledge; they are accessible to almost anyone in a manufacturing setting. For example, one of these tools might help you visualize where problems are happening most often, making it easier to decide where to focus your efforts. So, it's almost like having a set of basic instruments to measure and understand what’s going on.
These tools include things like checklists, diagrams that show how often certain issues occur, and charts that help you see relationships between different factors. They are designed to help teams collect and analyze information about their processes and products in a clear, visual way. By using these simple methods, people can identify patterns, spot areas for improvement, and make decisions based on actual facts, rather than just guesswork. They are, in a way, the building blocks for any serious effort to improve quality. They are very practical, you know, for daily use.
Learning to use these seven basic tools is often the first step for many people who want to become more involved in quality improvement. Organizations like ASQ, the largest society focused on quality, offer great resources to help you get a handle on them. They provide clear explanations and examples of how each tool works and how it can be put to use in real-world situations. Mastering these simple helpers can truly make a big difference in how effectively you can tackle challenges and drive better results in manufacturing. They are, quite simply, essential for anyone serious about making things well.
How Can You Start Applying Quality Quotes for Manufacturing Today?
If you're feeling inspired by the idea of making things better and want to start applying some "quality quotes for manufacturing" in your own work, where do you even begin? A great first step is to simply look at the resources that are already out there, designed to help people just like you. For instance, the ASQ website is a treasure trove of information, offering definitions, concepts, and even technical terms that make up the world of quality. They have an online glossary that can be incredibly helpful for getting familiar with all the specialized words and phrases. It’s like having a helpful dictionary right at your fingertips, which is very convenient.
You can also think about getting some formal recognition for your knowledge. For example, earning a Certified Quality Engineer (CQE) certification from ASQ shows that you've really mastered the principles of quality engineering. This kind of certification can open up new opportunities and give you a deeper grasp of how to improve processes and products. Joining a professional group like ASQ can also save you money on these certification exams, and it connects you with a wider community of people who share your interests. It’s a good way, you know, to boost your career.
Beyond formal learning, there are also tools that can give you immediate help. For example, ASQ offers an AI assistant called Quincy, which provides insights and access to a huge library of content. Quincy can help you solve quality challenges, give you recommendations, and even offer deeper looks into important topics like Lean and Six Sigma. This kind of immediate support means you don't have to figure everything out on your own. It's like having an expert available 24/7 to help you make sense of things and move forward. You can also connect with others by registering for an ASQ event, which is a great way to expand your network and share experiences. It’s a pretty comprehensive support system, actually.
This article has explored the crucial role of quality in manufacturing, distinguishing between quality assurance and quality control as different yet complementary approaches to ensuring product excellence. We've looked at how a higher level of quality goes beyond mere satisfaction, aiming to truly delight customers. The piece also touched upon the guiding influence of core quality principles, often encapsulated in simple sayings, in shaping workplace attitudes and fostering collaboration. We then discussed the importance of structured quality management systems (QMS) in driving continuous improvement and highlighted the tangible benefits of a strong quality focus, from happier customers to increased efficiency. Finally, we covered some fundamental tools and resources available, such as the seven basic quality tools and support from organizations like ASQ, including certifications and AI assistance, to help individuals and companies embark on or advance their journey toward consistent quality.
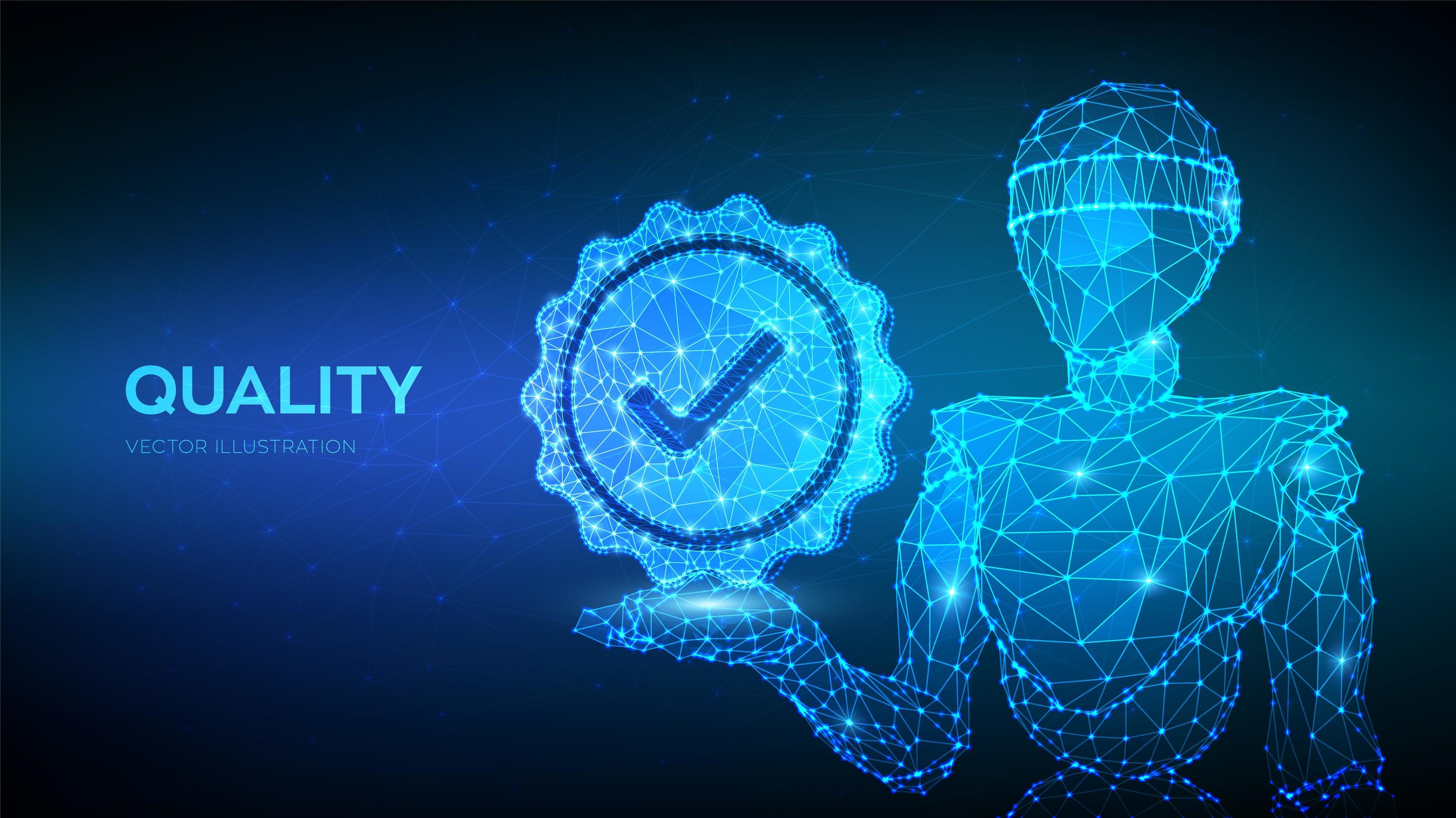
Quality. Standard Quality Control Certification Assurance. Guarantee

What is quality? Definition and examples - Market Business News
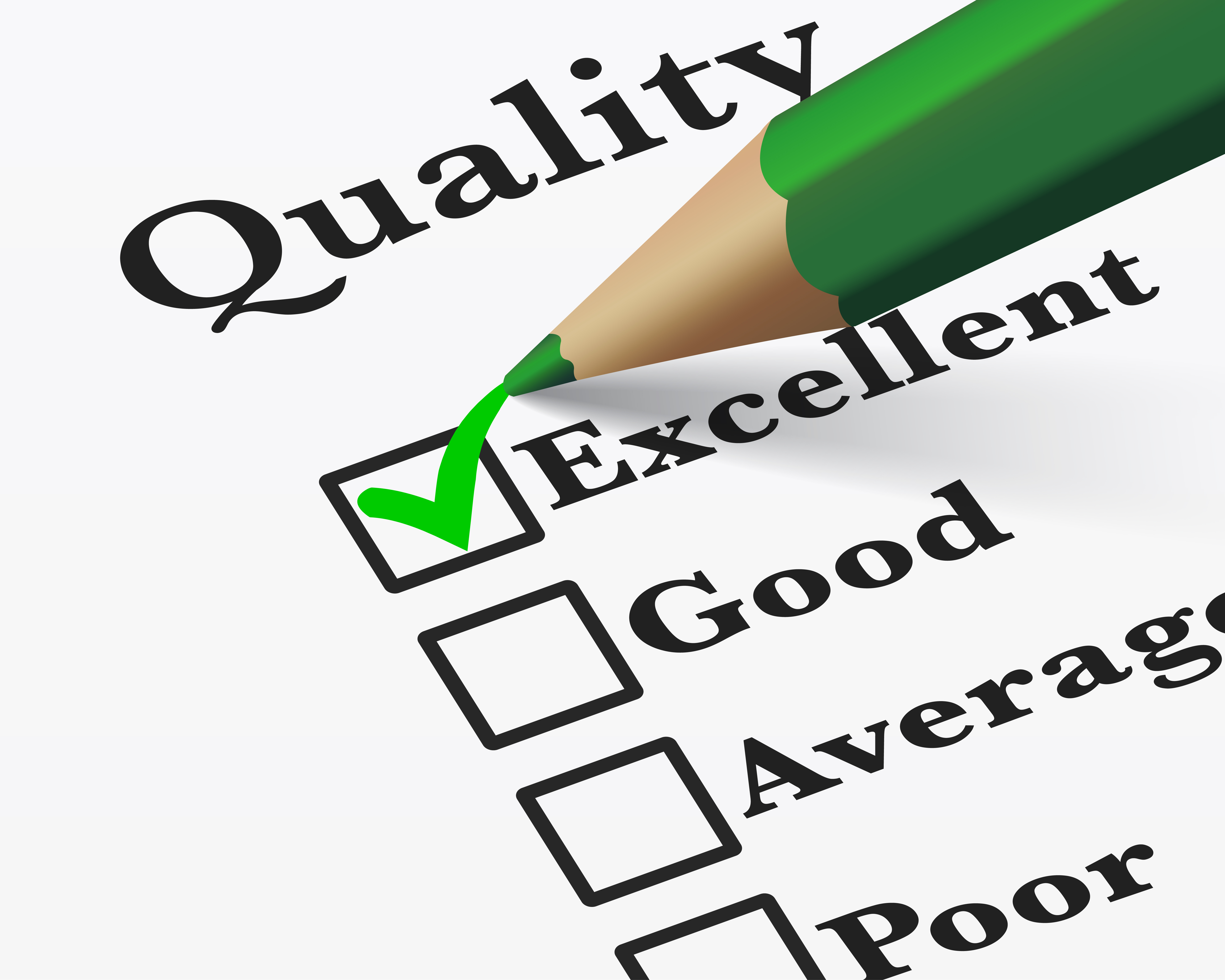
Quality - Blachford